We believe that every company has a responsibility to behave in a manner that is not detrimental to the environment. It is our policy to perform our operations with due regard to their effect on the environment. Consequently we are committed to meeting and wherever possible, surpassing the applicable environmental regulatory requirements and have been certified to the ISO14001:2015 Environmental Management System.
At every possible opportunity we reuse and recycle materials and at all times we endeavour to minimise the use of natural resources and the production of pollution and waste. Our continual aim is to send zero waste to landfill, with all waste being disposed of using environmentally friendly methods.
Each employee is given environmental training as part of their induction and made aware of the 3Rs the company follows, reduce, reuse and recycle. It is down to each individual to act in an environmentally responsible way. We also use a Kanban system, a Japanese system for reordering components, which prevents a build-up of large amounts of stock.
We support industry initiatives that are good for the environment including the International Ride to Work Week, where we help promote the benefits of commuting on Powered two Wheelers, including Motorbikes.
All employees are kept up to date with environmental issues and training sessions. We aim to create a culture of environmental awareness and continually strive for improvement in our environmental performance.
With regard to resources (water, gas, electricity and fuel) the company ethos is to be as economical as possible, switching off electrical equipment, PCs, lights, heaters when not necessary. We have replaced standard lighting with energy saving LED lighting. We use energy management software on key equipment so consumption of gas, electric and water can be closely monitored. Our company cars are economical and energy efficient.
To reduce the use of the raw materials in our processes, (foil, aluminium, steel, pallets, cardboard, cleaning cloths, paper and chemicals) we reuse where possible before disposal. In the Pre-Treatment of the foil and Etch Bay Area for the crash test barriers there has been investment in an Aqueous Washing plant to make the process more efficient and reduce the waste generated. Used water is passed through a Water Filtration System or Reverse Osmosis Unit which enables a pH7 to be restored so it can be used for our Etch bay area as part of our recycling initiative.
A recent project for individual bulk storage containers (IBCs) has enabled us to reduce the amount of chemicals we store, making handling easier and safer and reducing the risk of environmental contamination. The storage surface has been improved and the rain water run-off drainage has been fitted with an automated shut-off valve to stop any accidental spillage of chemicals entering the drains and eventually local streams and rivers, which would cause an ecological disaster.
Where possible our waste is recycled, with bins in the offices, canteens and on the shop floor. Encocam use certified Waste Management Suppliers for disposal of our waste using the latest technologies, like MRF (Materials Recovery Facility) and RDF (Refused Derived Fuel). All waste steel and aluminium from our processes are collected and sent to recycling plants. The chemicals used in our processes are disposed of as hazardous waste alongside regulations.
Encocam follows a 5S system, a Japanese organisational approach standing for sort, straighten, shines, standardise and sustain. Every workspace should be organised and include only the equipment required for the job, shadow boards are used for tool on the shop floor. It is a discipline for employees and encourages them to have standards to work to. It also helps reduce waste and improves efficiencies.
In 2017 Encocam won the EEF Future Manufacturing Award for Environmental Achievement for the South east Region and in 2021 we were named finalists in the SME Huntingdonshire Business Awards in the Sustainability category.
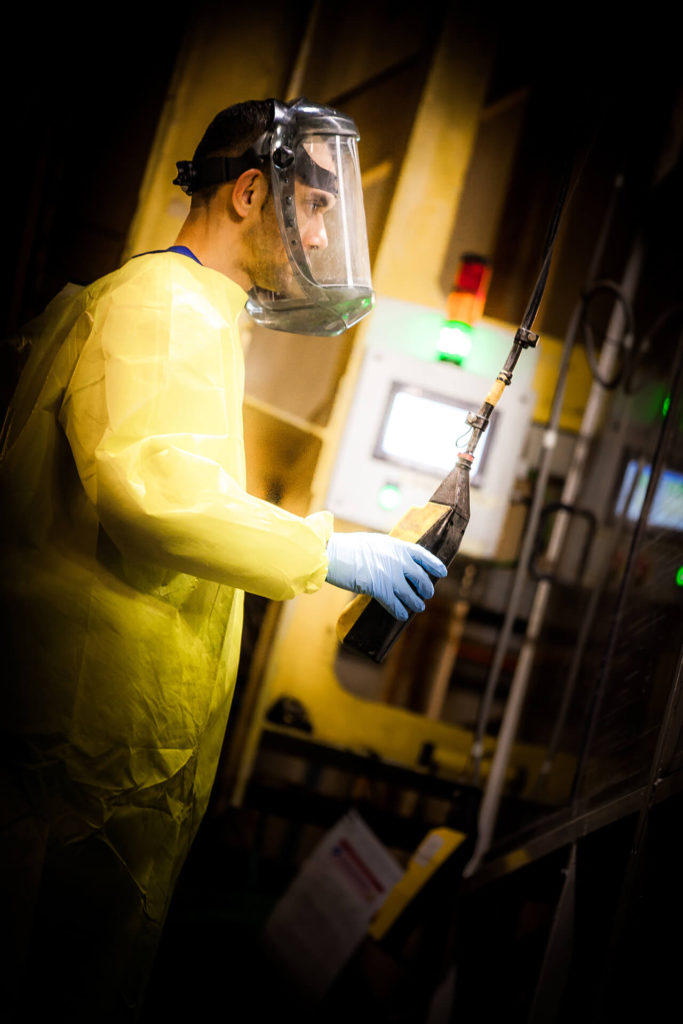
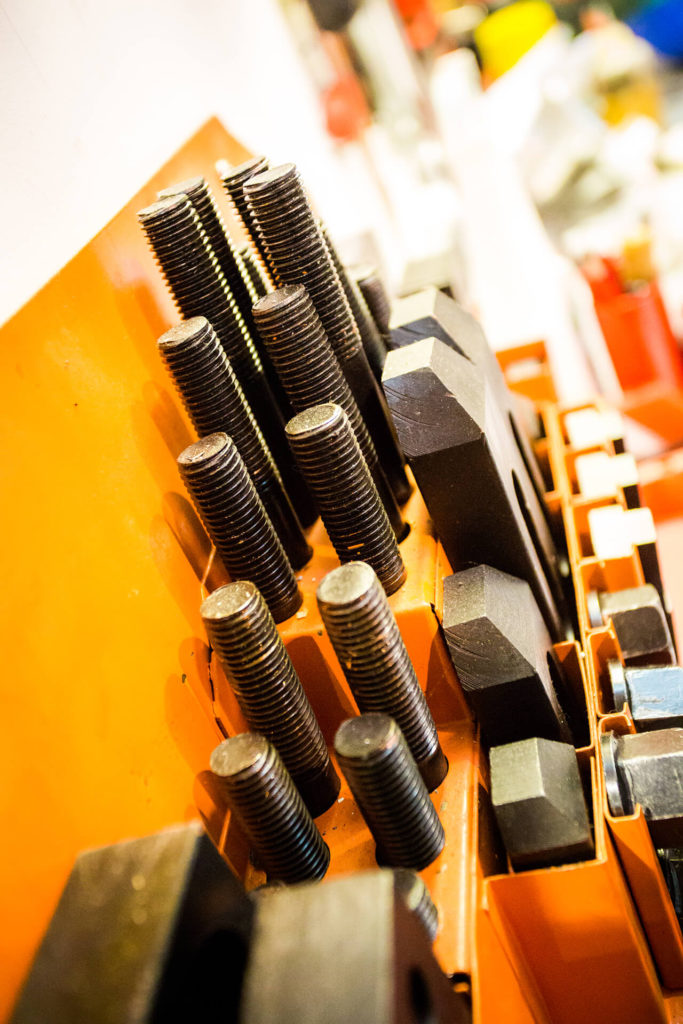
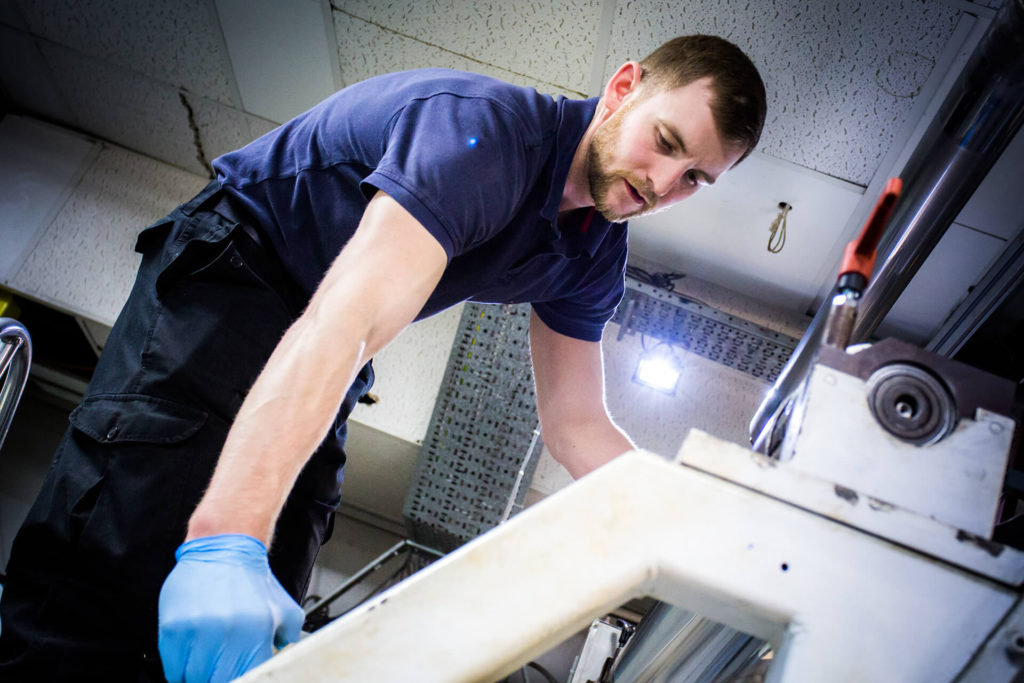