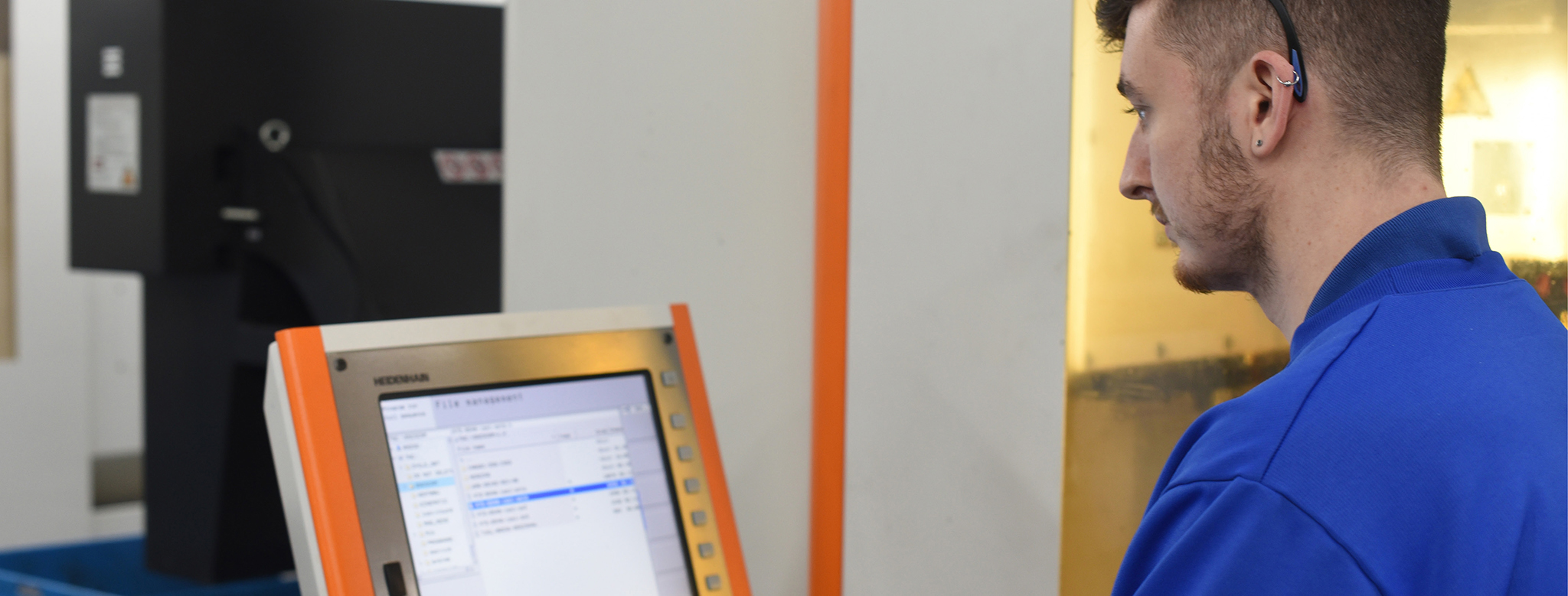
Interview with an Apprentice
11 November 2021We interviewed Tom, a CNC Apprentice in our Stonehill Engineering division, as he reflects on what he has learnt during his apprenticeship and his plans for the future:
Why did you want to be an apprentice?
I didn’t consider an apprenticeship initially as most people I knew were focused on university. I went to sixth form but found all the coursework hard to manage – I prefer the practical side of learning. I made the difficult decision to drop out and took the first job I was offered at a coffee shop chain. This was great for increasing my confidence with talking to customers, but I wanted a plan for the future and my family suggested I consider an apprenticeship.
Why did you choose a Machining apprenticeship?
Before I applied, I looked on the company website and researched the role of a CNC machine operator. I watched lots of videos and thought it sounded really interesting. The fact it was a 4-year apprenticeship was also reassuring – if it takes 4 years to become qualified then it must be a big deal!
I wasn’t sure about working in a factory but as part of my interview I was given a tour and looked around all the machines, which were impressive. I was taken through the different stages involved in creating precision parts. I was also shown the computer programming area which was really interesting. I’d thought about being a design engineer when I was younger, so it was fascinating to see how all the different parts of the process fit together.
When did you join Stonehill Engineering?
I started as a CNC apprentice in June 2018 a few months before my college course began in September. This enabled me to get ahead with some of the practical aspects of my course. When I started college, I was one of the few who had some experience using the machines.
What qualification are you studying for?
I completed my Level 2 in Machining and am about to finish my Level 3 qualification at Cambridge Regional College (CRC). I have an Assessor who I communicate with regularly. There are so many different units you have to complete as part of your course, they make sure you are up to date and know what you need to do next. I don’t need to go into college now but at the start I went in 2 days a week, this decreased to 1 day as I progressed.
How did you find learning something completely different?
At Stonehill Engineering you are not put straight onto a machine, it’s expensive equipment and you are in control of whether it goes right or wrong, so you need to build up your confidence. I spent the first few weeks shadowing different people while they explained what they were doing. There’s a lot to learn and initially I thought: “There is no way I’m going to be able to do this!”, but over time you start to remember.
One of the ways that helped me to learn was when they broke down the whole process one task at a time. I was asked to take ownership of a small part of this process. Every time I did that task, they would watch to make sure it was correct and give me feedback. If I asked a question that had previously been answered I was challenged to figure out the solution myself.
Everyone in the team has varying levels of experience. One person had just finished his own apprenticeship and understood what I needed to learn and was keen to help. Other team members have years of experience and it’s great to have access to that knowledge when you need to ask more obscure questions!
What is a typical day like?
Very busy! We have a lot of work coming in that we need to make sure we complete on time. You must be efficient and always stay one step ahead, so as a process completes you have everything ready to start the next one.
Currently I operate the 5-axis machines creating complex parts. The term 5-axis refers to the number of directions the cutting tool can move and means you can approach the part in all directions. I get involved in making all different types of precision parts for both internal and external customers. We produce a lot of items for crash test dummies and pedestrian legforms used in automotive safety testing. Recently we’ve been working on parts for a British-built motorcycle.
What new skills have you developed?
At first, I was taught how to use the 3-axis machine and once I felt confident I showed enthusiasm and put myself forwards to help with the 5-axis. As you improve you are moved onto the next step, as long as that’s what you feel comfortable with.
Apart from machinery skills, I’m also much better at communication now. You can’t afford not to be vocal if you see something that hasn’t been done correctly. If you make a mistake yourself, you need to be up front about it as there can be a knock-on effect for customer deadlines if it’s not sorted out straight away. It’s better to speak up and then show you can do better next time.
What do you enjoy most about being an apprentice?
I enjoy many aspects. I like how practical and hands on it is and I like the hours as my weekends are kept free. Although your work is monitored there is a lot of independence and you are not micro-managed – as long as you meet your daily targets you can go at your own pace.
Has anything surprised you about your apprenticeship?
Being a CNC Apprentice offers fantastic career progression. It’s a job where there is always a path in front of you and always more you can do. I thought I would have to finish my apprenticeship before I was trained on the 5 axis machines, but if you are keen and they think you are ready, then you are given the opportunity.
With an apprenticeship you earn straight away. You might not start on the highest salary, but you see incremental increases as you progress and by the time I finish my course I will be earning an amount that I didn’t think would be available to me at this age, without going to university.
How has Encocam supported you?
It feels like the company takes responsibility for your apprenticeship, providing most of your learning in the workplace rather than relying on the college. They are very relaxed about the time you take to attend lessons, for example if you need to go in for an extra day. During the coronavirus pandemic the practical side at college was really restricted. When they asked us to come in for catch-up sessions the company had no issue with this, it was never questioned.
It’s a good environment for an apprentice to work in as everything is done by the book with no short cuts. When you are first learning you are instructed to take your time and ask questions to make sure you get it right. We have a good team and our team leader puts your interests first and is motivated to help people who he sees are trying to succeed.
What future plans and ambitions do you have?
I want to keep pushing forwards and I would like to do my level 4 qualification, which involves more offline programming. I feel like I now have a career with options available to me for progression and skills that are of value to my company, something I didn’t think I had when I decided to leave sixth form.
What advice would you pass onto someone who is thinking of becoming an apprentice?
Remember university is not the only option for finding a career. As an apprentice you don’t need to have the same qualifications as someone who goes to university, you just need to show the right characteristics – that you want to work there, are willing to learn and will put in the effort.
Research the title of the apprenticeship you are interested in and what comes out of it at the end as you might be surprised about where it could lead.
Also, don’t focus on waiting until September when college starts to do an apprenticeship, join when you can and start getting experience straight away.
Is there anything else you would like to highlight?
Don’t ever feel like you are not the type of person who would fit into a factory environment. It’s the right balance of professional but also relaxed. There are all different types of people working here and everyone is very accepting. I have been made to feel really welcome.
If you would like to find out more about the variety of apprenticeships available at Encocam, please contact us.